The Scientific Research Behind Porosity: A Comprehensive Overview for Welders and Fabricators
Recognizing the detailed devices behind porosity in welding is crucial for welders and fabricators striving for remarkable craftsmanship. As metalworkers explore the depths of this phenomenon, they uncover a globe governed by various factors that affect the development of these tiny spaces within welds. From the composition of the base materials to the details of the welding procedure itself, a plethora of variables conspire to either aggravate or relieve the visibility of porosity. In this comprehensive guide, we will certainly untangle the scientific research behind porosity, discovering its effects on weld quality and unveiling progressed strategies for its control. Join us on this trip through the microcosm of welding imperfections, where accuracy satisfies understanding in the quest of perfect welds.
Understanding Porosity in Welding
FIRST SENTENCE:
Evaluation of porosity in welding discloses essential understandings into the integrity and quality of the weld joint. Porosity, identified by the presence of tooth cavities or gaps within the weld metal, is a typical worry in welding processes. These spaces, otherwise correctly attended to, can compromise the structural honesty and mechanical properties of the weld, resulting in possible failings in the finished product.

To find and evaluate porosity, non-destructive screening methods such as ultrasonic testing or X-ray examination are often employed. These techniques enable the identification of interior issues without jeopardizing the stability of the weld. By examining the dimension, shape, and distribution of porosity within a weld, welders can make educated decisions to enhance their welding procedures and attain sounder weld joints.
Factors Influencing Porosity Formation
The incident of porosity in welding is affected by a myriad of aspects, varying from gas protecting performance to the details of welding criterion setups. One critical factor contributing to porosity formation is inadequate gas shielding. When the securing gas, typically argon or carbon dioxide, is not effectively covering the weld pool, climatic gases like oxygen and nitrogen can infect the liquified metal, resulting in porosity. Furthermore, the cleanliness of the base products plays a substantial function. Pollutants such as rust, oil, or moisture can evaporate throughout welding, producing gas pockets within the weld. Welding specifications, including voltage, current, take a trip rate, that site and electrode type, additionally influence porosity formation. Utilizing incorrect settings can create extreme spatter or heat input, which subsequently can lead to porosity. The welding technique used, such as gas metal arc welding (GMAW) or secured metal arc welding (SMAW), can influence porosity formation due to variants in heat circulation and gas protection. Recognizing and managing these factors are essential for minimizing porosity in welding procedures.
Results of Porosity on Weld High Quality
The presence of porosity also deteriorates the weld's resistance to corrosion, as the trapped air or gases within the gaps can respond with the surrounding atmosphere, leading to deterioration over time. Furthermore, porosity can impede the important link weld's ability to withstand stress or influence, additional jeopardizing the total quality and reliability of the bonded structure. In critical applications such as aerospace, automotive, or architectural buildings, where safety and resilience are critical, the detrimental results look these up of porosity on weld high quality can have extreme repercussions, emphasizing the relevance of decreasing porosity via appropriate welding techniques and treatments.
Techniques to Decrease Porosity
To improve the quality of bonded joints and make sure structural stability, welders and fabricators use particular strategies targeted at lowering the development of voids and dental caries within the material throughout the welding procedure. One efficient approach to reduce porosity is to make certain appropriate product preparation. This consists of comprehensive cleansing of the base steel to remove any kind of contaminants such as oil, oil, or moisture that might add to porosity formation. Furthermore, making use of the appropriate welding criteria, such as the appropriate voltage, present, and take a trip speed, is important in stopping porosity. Preserving a consistent arc length and angle during welding additionally helps in reducing the probability of porosity.

Making use of the ideal welding strategy, such as back-stepping or using a weaving movement, can also aid disperse heat equally and minimize the possibilities of porosity formation. By executing these techniques, welders can effectively decrease porosity and create premium welded joints.
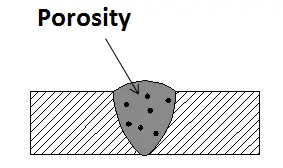
Advanced Solutions for Porosity Control
Applying innovative technologies and innovative techniques plays a critical duty in achieving premium control over porosity in welding procedures. One advanced option is using innovative gas blends. Shielding gases like helium or a combination of argon and hydrogen can help in reducing porosity by giving much better arc security and enhanced gas insurance coverage. Furthermore, using sophisticated welding methods such as pulsed MIG welding or modified ambience welding can also assist mitigate porosity problems.
Another sophisticated remedy involves using sophisticated welding tools. As an example, utilizing devices with built-in features like waveform control and sophisticated source of power can boost weld quality and decrease porosity dangers. The implementation of automated welding systems with precise control over parameters can considerably reduce porosity problems.
Moreover, including sophisticated tracking and assessment technologies such as real-time X-ray imaging or automated ultrasonic screening can help in finding porosity early in the welding process, enabling for instant corrective actions. Overall, incorporating these innovative options can considerably boost porosity control and boost the general high quality of welded parts.
Verdict
In conclusion, recognizing the science behind porosity in welding is essential for welders and makers to create top quality welds - What is Porosity. Advanced remedies for porosity control can even more boost the welding process and make certain a strong and trusted weld.
Comments on “Professional Recommendations on What is Porosity in Welding and Just How to Resolve It”